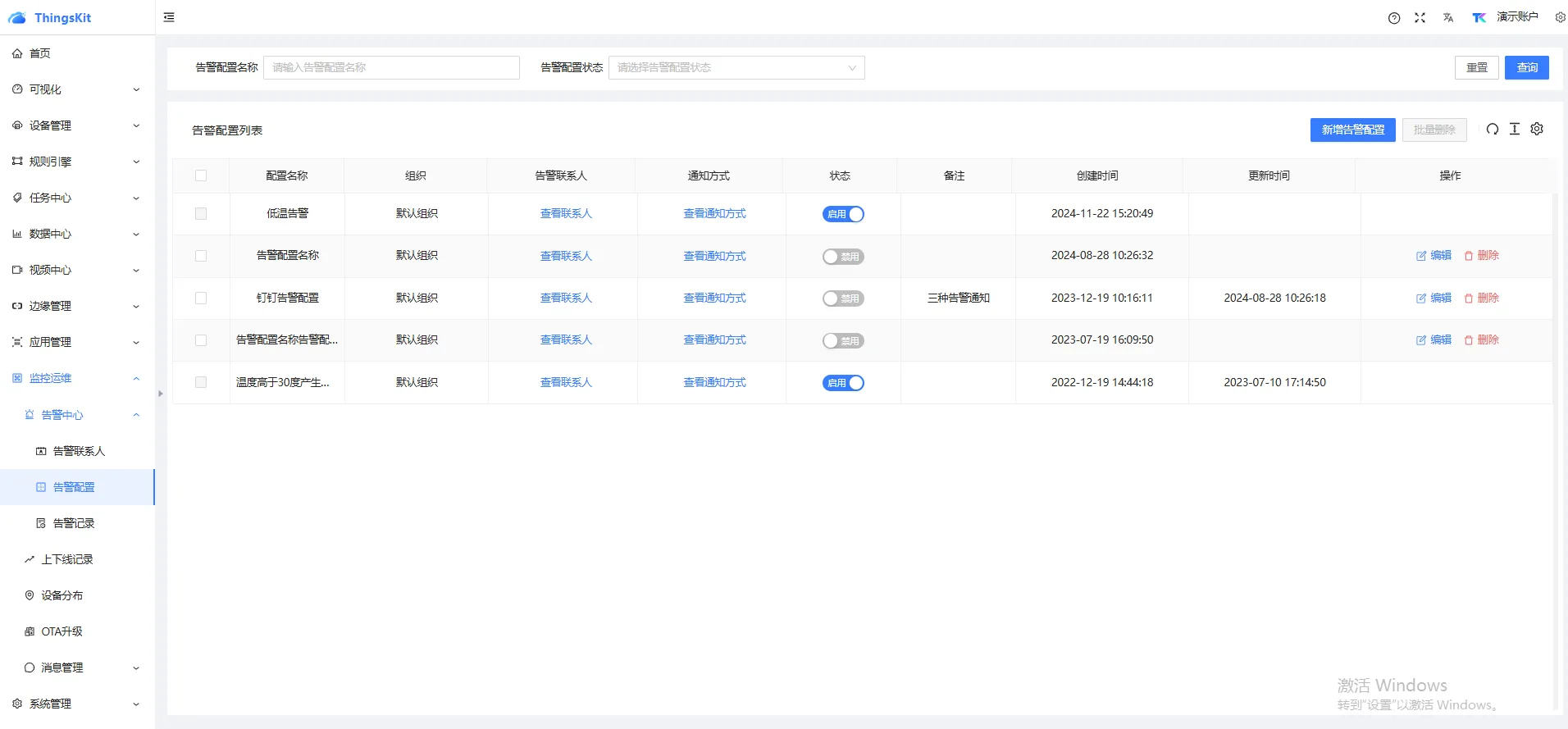
在现代工业生产中,设备的稳定运行对于保障生产效率和产品质量至关重要。而工业设备预测性维护作为一项关键技术,其算法模型的演进历程见证了工业智能化发展的脚步。
早期的预测性维护主要依赖于基于经验和统计的模型。比如,通过统计设备在一定时间内的故障频率、运行时长等数据,采用简单的统计学方法如正态分布、泊松分布等来预测设备故障的可能性。这种方法虽然在一定程度上能够提供参考,但对于复杂的工业设备和多变的运行环境,往往显得力不从心。
随着计算机技术的发展,基于物理模型的预测性维护方法逐渐兴起。这种模型以设备的物理原理为基础,利用热力学、机械学等物理方程来描述设备的运行状态。例如,对于电机设备,通过建立电机的电磁场模型和热力学模型,结合电机的电流、电压、温度等实时监测数据,可以更准确地预测电机的故障。然而,构建物理模型需要深入的领域知识和大量的实验数据,且对于一些复杂的设备或系统,精确建模存在很大困难。
近年来,机器学习和人工智能技术的飞速发展为工业设备预测性维护带来了新的变革。监督学习式算法如支持向量机、随机森林等被广泛应用。这些算法利用大量标注了故障状态的设备运行数据进行训练,学习设备状态与故障之间的映射关系例如。,通过对机床加工过程中刀具的磨损数据、切削参数数据等进行训练,随机森林算法可以快速准确地判断刀具的磨损程度并预测其失效时间。
深度学习的发展进一步推动了预测性维护算法模型的进步。卷积神经网络(CNN)和循环神经网络(RNN)及其变体长短期记忆网络(LSTM)等在处理设备的时序数据和图像数据方面表现出色。以工业机器人视觉检测为例,CNN 可以对机器人的视觉传感器采集的图像进行数据分析,及时发现零部件的表面缺陷和磨损情况。而 LSTM 对于设备的振动信号、电流信号等时序数据具有良好的处理能力,可以捕捉到设备状态随时间的变化趋势,从而更精准地预测故障的发生。
当前,工业设备预测性维护的算法模型正朝着融合多种技术的方向发展。例如,将物理模型与机器学习算法相结合,利用物理模型提供先验知识,机器学习算法进行数据驱动的优化和补充,以提高预测的准确性和可靠性。同时,随着物联网技术的普及,大量的设备运行数据能够实时传输和共享,这为算法模型的训练和优化提供了更丰富的数据资源,使得预测性维护更加及时、智能和高效。
可以预见,未来工业设备预测性维护的算法模型将在不断演进中,更加紧密地与工业实际需求相结合,为工业生产的稳定、高效和安全提供更有力的支持。